Laseroptiken werden je nach Spezifizierung der emittierten Wellenlänge mit unterschiedlichen dielektrischen Beschichtungen versehen. Motivation für das Projekt SILA waren Fehler in der Grenzfläche zwischen der Beschichtung und dem Grundglas, die in der Endkontrolle als „wolkiger Belag“ bezeichnet wurden. Das Ziel des Projekts war es, die Fehlerursachen für Grenzflächeneffekte zu identifizieren und abzustellen.
Im Projekt wurden die Fehlerbilder in der Endkontrolle klassifiziert. Eine Analyse der Fertigungsdurchläufe ergab zwei Prozessketten. In diesen wurde die mögliche Entstehung von Oberflächenfehlern verortet. Parallel wurde eine digitale Verfolgung von Fertigungsaufträgen aufgebaut. Als kritischer Schritt wurde die automatische Waschanlage identifiziert. Die hier gefundenen Fehlerbilder nach der Reinigung wurden mit denen in der Endkontrolle abgeglichen. Da Oberflächeneffekte vor der Beschichtung einer Analyse leichter zugänglich sind als nach der Beschichtung, wurden diejenigen Fehler zuerst untersucht, die sowohl nach der Reinigung in der Waschanlage als auch in der Endkontrolle gefunden wurden.
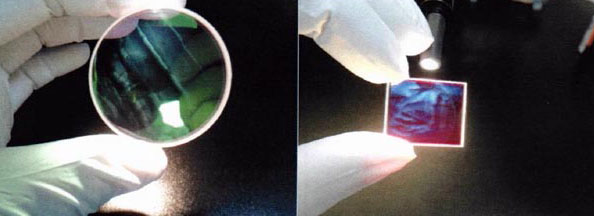
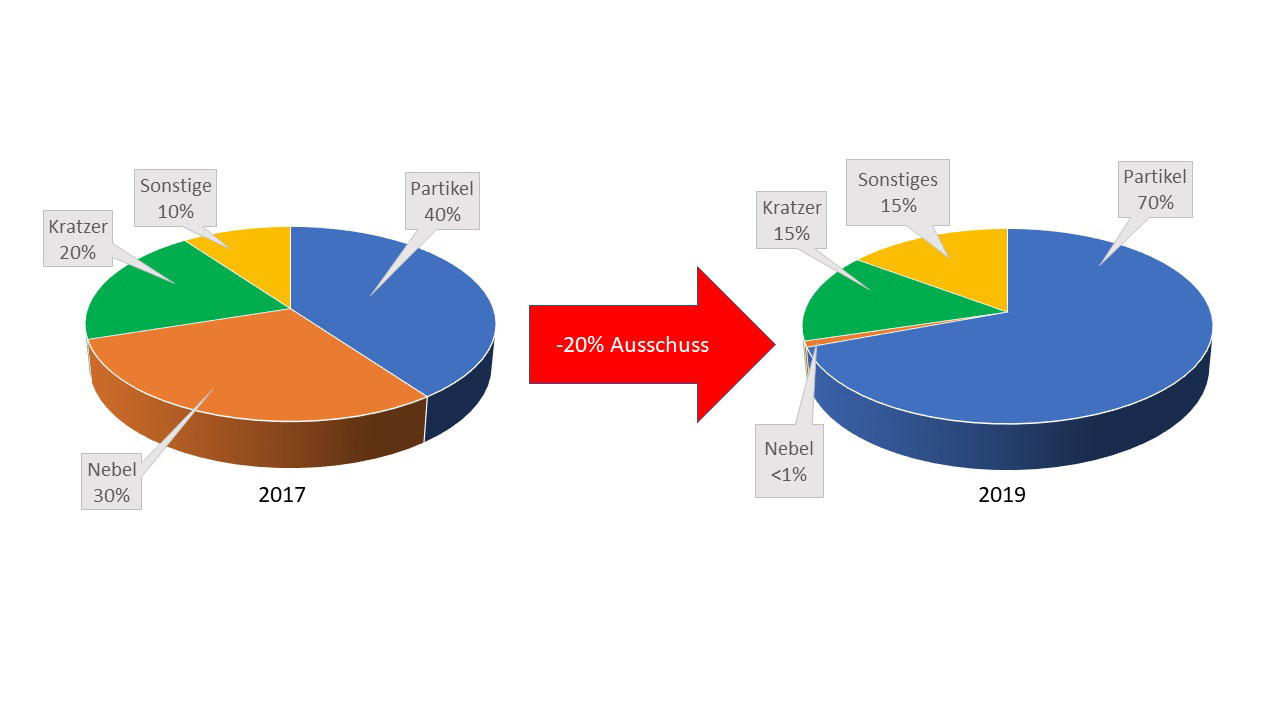
rechts: Fehlerverteilung am Beginn und am Ende des Projektes (Quelle: Laser Components GmbH)
Durch die Analyse der Fehler mit dem Lichtmikroskop, dem Raman-Mikroskop und dem Rasterelektronenmikroskop wurden den vorab klassifizierten fünf Fehlerarten Ursachen aus der Fertigung zugeordnet. Zum Beispiel konnte der wolkige Belag (siehe Bild) einer Verschleppung in der Reinigungsanlage zugeordnet werden. Für spezifische Fehlerbilder wurden Abstellmaßnahmen definiert. Die Wirksamkeit des Fehlerkataloges und der Abstellmaßnahmen zeigte sich gegen Ende des Projektes, als ein „behobener“ Fehler erneut auftrat und zielgerichtet behoben werden konnte.
Parallel zu der Fehleranalyse in der Fertigung wurde ein Test aufgebaut, um die Wirkung der Grenzflächenfehler im Einsatz prüfen zu können.
Im Projekt kooperierten die Firmen Laser Components und Toptica sowie die Technische Hochschule Deggendorf. Assoziierter Partner war die Firma Coherent.