Optimierung von Temperierkanälen: Die schier grenzenlose Designfreiheit der additiven Verfahren stellt den Werkzeugkonstrukteur vor große Herausforderungen. Gestalt, Lage und Durchmesser der Kühlkanäle wollen gut überlegt sein – digitale Modelle können bei der Konstruktion helfen.
Beim Spritzgießen werden zur Kühlung von Werkzeugformeinsätzen Temperiersysteme eingesetzt. Dazu finden derzeit neben konventionell gebohrten auch durch das Strahlschmelzen hergestellte, konturnahe Temperierkanäle Verwendung. Letztere können an den Verlauf der Werkzeugkavität angepasst werden und ermöglichen daher eine verbesserte Wärmeregulierung (vgl. obere Abbildung). Die geometrischen Freiheiten bei der Auslegung konturnaher Temperierkanäle hinsichtlich ihrer Gestalt und Lage stellen den Konstrukteur vor hohe Herausforderungen.
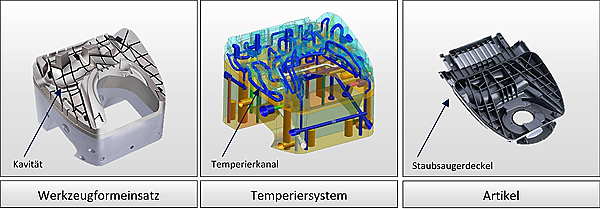
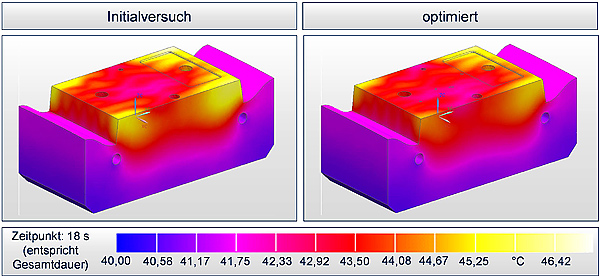
rechts: Segmentdarstellung der Temperaturverteilung beim Nominalversuch und optimiert (Quelle: Hofmann Innovation Group GmbH)
Zielsetzung des Forschungsvorhabens war die Entwicklung einer Prozesskette für die simulationsgestützte Analyse und Auslegung von Temperiersystemen. Die dazugehörige Zielgröße bestand in der Reduzierung von Temperaturgradienten entlang der Kavitätsoberseite und die damit verbundene Verringerung von Verformungen des gespritzten Artikels nach dem Entformen. Das im Projekt entwickelte Vorgehen sieht vor, das Temperiersystem bei der Konstruktion des Werkzeugformeinsatzes in Abschnitte zu unterteilen. Dadurch war die abschnittsweise Vorgabe der zu optimierenden Kanaldurchmesser möglich. In einer darauf folgenden Spritzgießsimulation konnte das Temperaturfeld des Artikels berechnet und als Randbedingung anschließend in einer gekoppelten thermischen Fluidsimulation verwendet werden. In der Berechnung wurde vorwiegend der Abkühlvorgang unter Berücksichtigung der Strömungsverhältnisse im Temperiersystem betrachtet.
Durch zahlreiche Optimierungszyklen ist ein verbesserter Parametersatz für die Kanaldurchmesser zum Erhalt einer homogeneren Temperaturverteilung an der Werkzeugoberseite ermittelt worden. Ausgehend von dem ursprünglichen Parametersatz konnte für das betrachtete Testbauteil durch die Optimierung der Kanaldurchmesser der Temperaturgradient an der Werkzeugoberseite um 13,7 % reduziert werden (vgl. untere Abbildung).