Die konventionellen technologischen Konzepte für die Fertigung großvolumiger Urformwerkzeuge sehen die Umsetzung eines Temperiersystems durch geradlinige Bohrungen für Kühlkanäle vor. Damit ist eine Werkzeugtemperierung, die optimal an Bauteilanforderungen angepasst ist, nicht möglich.
Das Ziel dieses Projektes war die Entwicklung eines Technologiekonzeptes zur Herstellung großvolumiger Urformwerkzeuge mit anforderungsgerechter Temperierung und herausragenden, funktionellen Eigenschaften.
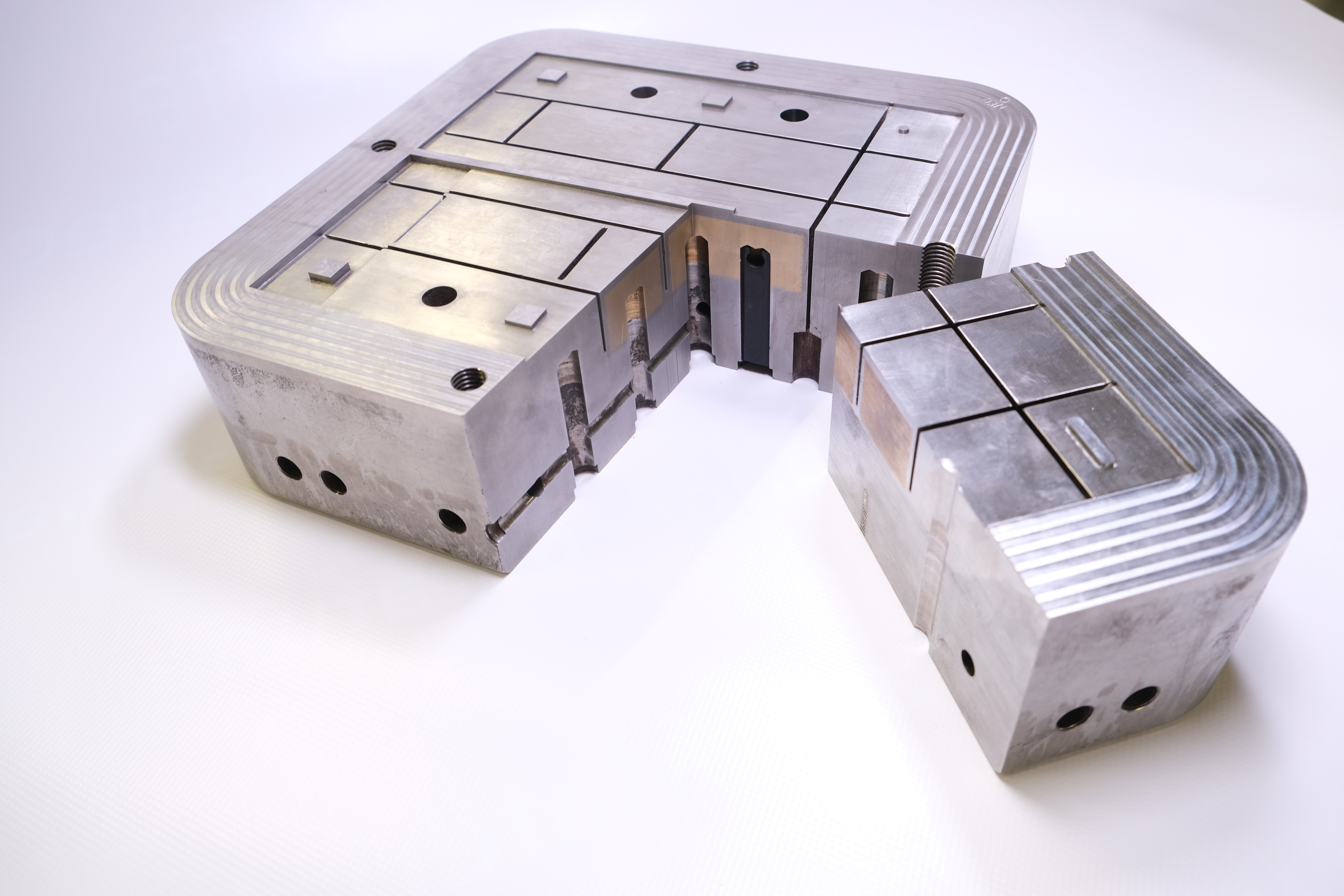
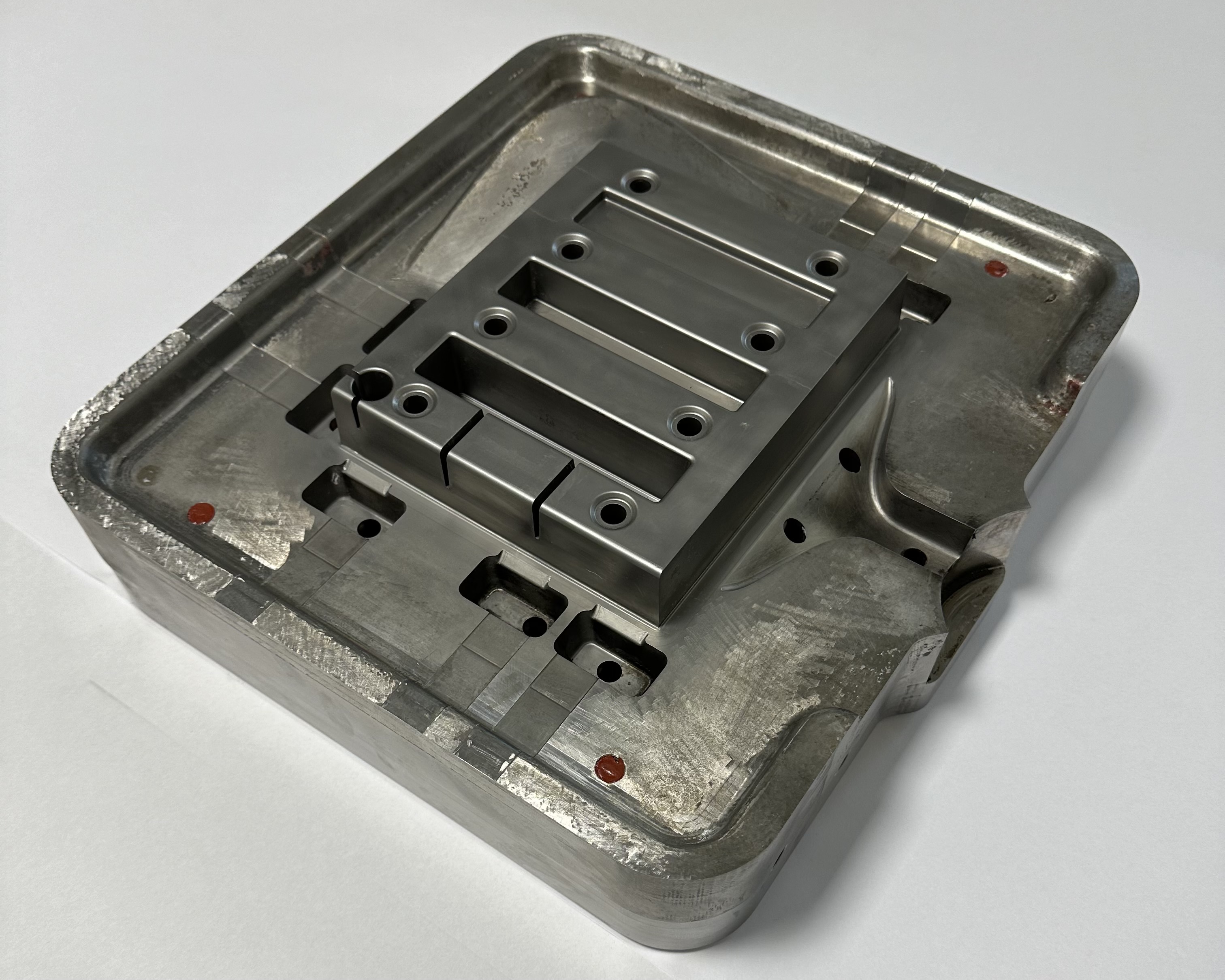
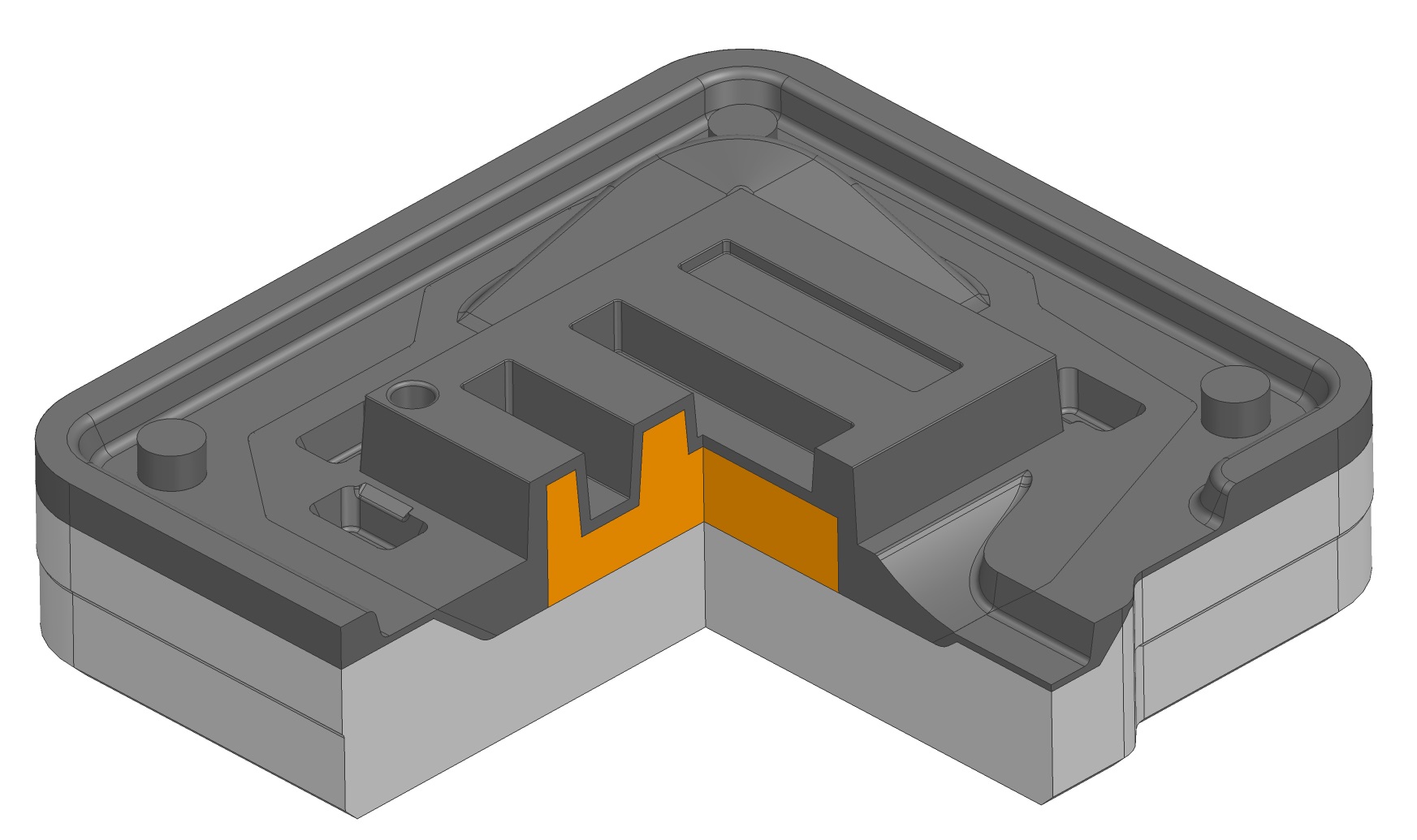
Der technologische Kern des Projektes beinhaltete eine funktionale Trennung von verschiedenen Werkzeugbereichen, die durch die Kombination additiver (auftragender) und subtraktiver (abtragender) Fertigungsverfahren nacheinander aufgebaut werden. Dabei sorgen im Inneren eines Werkzeugs Kanäle für die Führung des Temperiermediums in Kombination mit Wärmeleitungsschichten aus Materialen mit hoher Wärmeleitfähigkeit für die anforderungsgerechte Temperierung. Durch additive Fertigung können die Arbeitsflächen von Werkzeugen aus besonders harten, verschleißwiderstandsfähigen Materialien aufgebracht werden.
Für die Umsetzung der Projektidee wurde eine hybride Fertigungsprozesskette von großvolumigen Werkzeugen, basierend auf der Kombination von Fräsen mit den additiven Fertigungsverfahren, entwickelt und erprobt. Als additive Fertigungsverfahren kamen Laser-Pulver-Auftragsschweißen (LMD) sowie Drahtauftragsschweißen (WAAM) zum Einsatz.
Das Technologiekonzept für die Auslegung und Fertigung einer anforderungsgerechten Temperierung konnte durch die Herstellung und den Einsatz von Spritzguss- und Druckgusswerkzeugen unter serienähnlichen Bedingungen validiert werden. Es wurde eine Zykluszeitreduktion von 20 % bis 40 % bei gleichbleibender oder verbesserter Bauteilqualität erreicht.