Selektives Lasersintern (SLS) ermöglicht komplexe Bauteile mit hochgradiger Geometriefreiheit. Insbesondere ein Anbinden dieser an Serienbauteile kann dem steigenden Trend des Customizings folgen. Zur Nutzung von SLS Bauteilen in Baugruppen fehlen derzeit Erkenntnisse zur Realisierung dauerhafter und hochbelastbarer Verbunde.
Ziel des Projekts war die Erarbeitung der Wirkzusammenhänge zwischen Material, Fertigungseinfluss, Fügeprozess und resultierenden Verbundeigenschaften und darauf aufbauend die Aufstellung von Fügeempfehlungen.
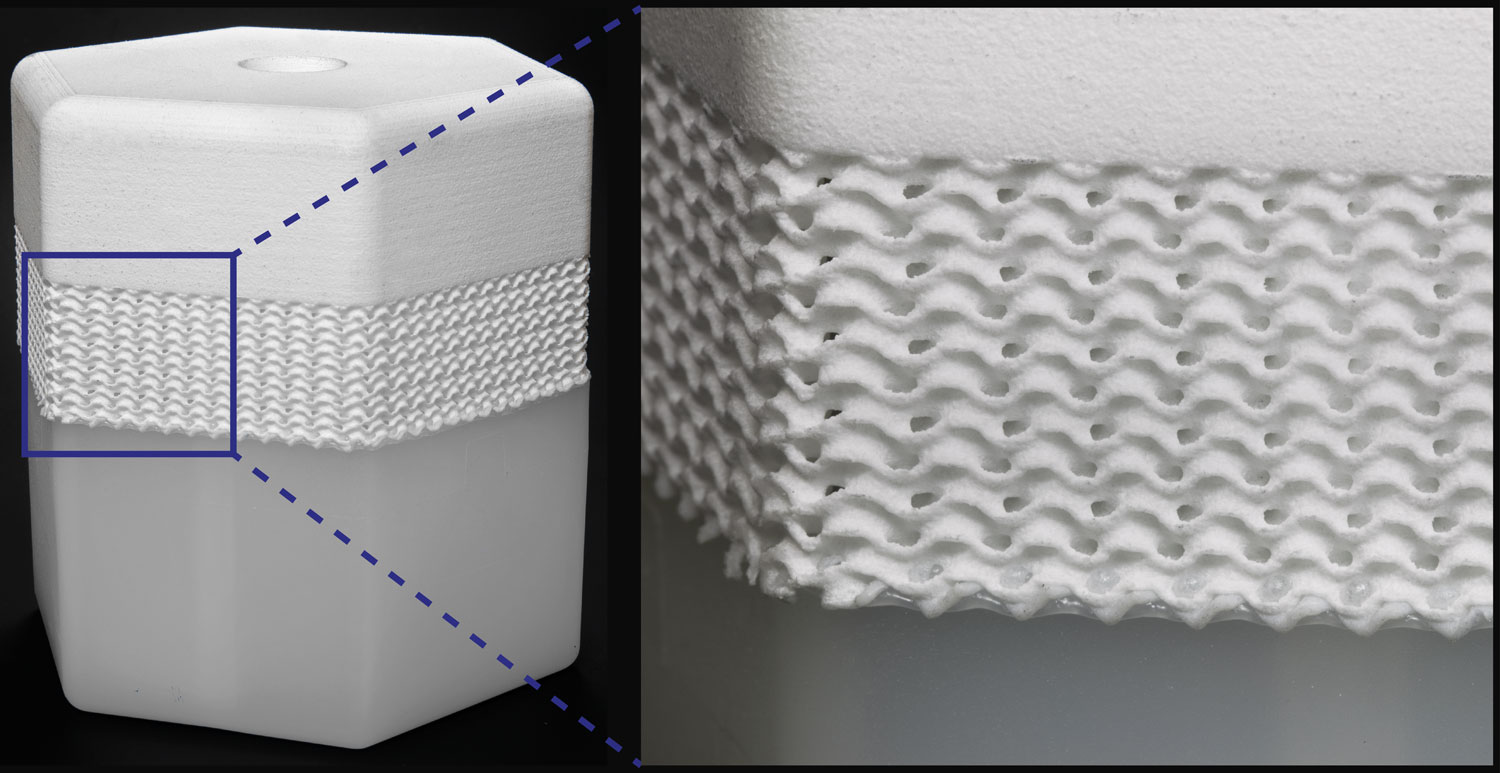

rechts: Infrarotgefügte individualisierte BMW MINI Komponenten: Spritzguss Blinker-Element mit SLS-Komponente (links), SLS-Armaturenbrettdekorleiste (rechts) (Quelle: Lehrstuhl für Kunststofftechnik, Friedrich-Alexander-Universität Erlangen Nürnberg)
Mittels einer angepassten Prozessführung sind hohe Festigkeiten für SLS-SLS Verbindungen sowie Verbindungen zwischen SLS und unverstärkten wie auch faserverstärkten Spritzguss (SG) Bauteilen erreichbar. Haupteinfluss des SLS Verfahrens auf das Infrarotschweißen ist die Aufbaurichtung und die hieraus resultierende Oberflächenrauheit und Porosität. Das Vibrationsschweißen ist weitgehend unabhängig von den SLS Parametern. Auffällig ist dagegen eine erhöhte Fügetemperatur aufgrund der erhöhten Kristallinität und Steifigkeit der SLS Bauteile.
Die Nahtmorphologie ist für SLS Bauteile deutlich abweichend zu konventionellen Schweißverbindungen, ein typischer Mehrschichtaufbau ist nicht erkennbar. Zudem ist die im Infrarotschweißen resultierende Wärmeeinflusszone erhöht bzw. die im Vibrationsschweißen resultierende Schmelzeerzeugung reduziert. Dies konnte den werkstofflichen wie auch fertigungsbedingten Unterschieden zwischen SLS und SG zugeordnet werden.
Vorteile für ein Anbinden komplexer SLS an SG Bauteile weist aufgrund der reduzierten Querbelastung das Infrarotschweißen auf. Mittels eines entwickelten Universal-Schweißwerkzeugs basierend auf SLS Spannelementen wurde zudem eine wirtschaftliche Fertigung auch für Einzelbauteile ermöglicht.