Mit dem raschen Voranschreiten der Entwicklungen im Bereich des autonomen Fahrens ändern sich auch die Ansprüche, die der Kunde an den Innenraum seines Fahrzeuges stellt. Der Fahrgastraum wandelt sich zu einer Mischung aus Büro und Wohnzimmer und so entwickelt sich auch das Interieur mit und geht den Schritt in Richtung Seamless-Surface, umfangreicher Funktionsintegration und „Wohlfühl“-Haptik.
Im von der Bayerischen Forschungsstiftung geförderten Forschungsprojekt SenseSkin entwickelte ein breit aufgestelltes Konsortium mit Partnern aus Industrie und Wissenschaft einen einer Handablage entlehnten Technologiedemonstrator für den Innenraum der Zukunft.
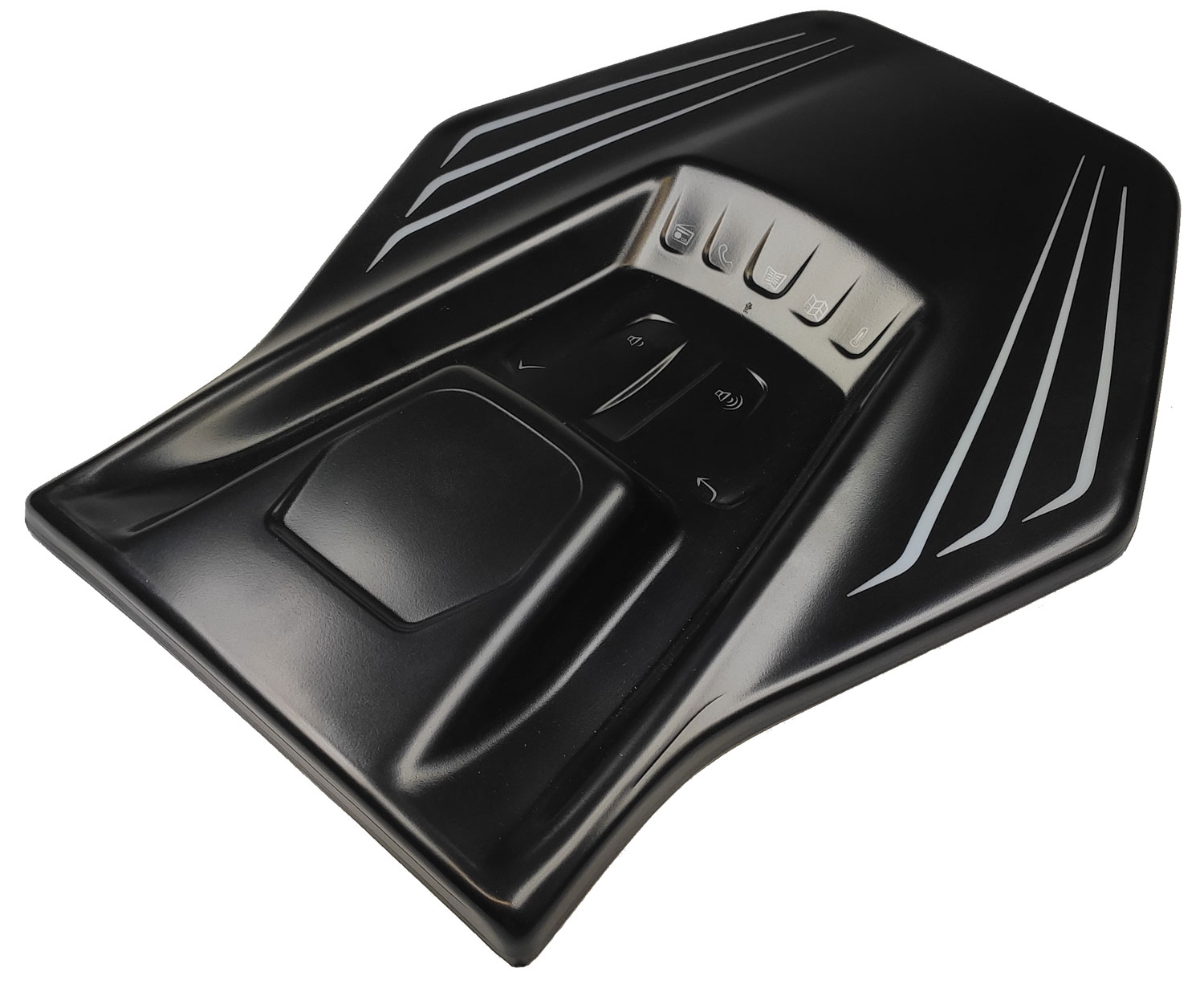
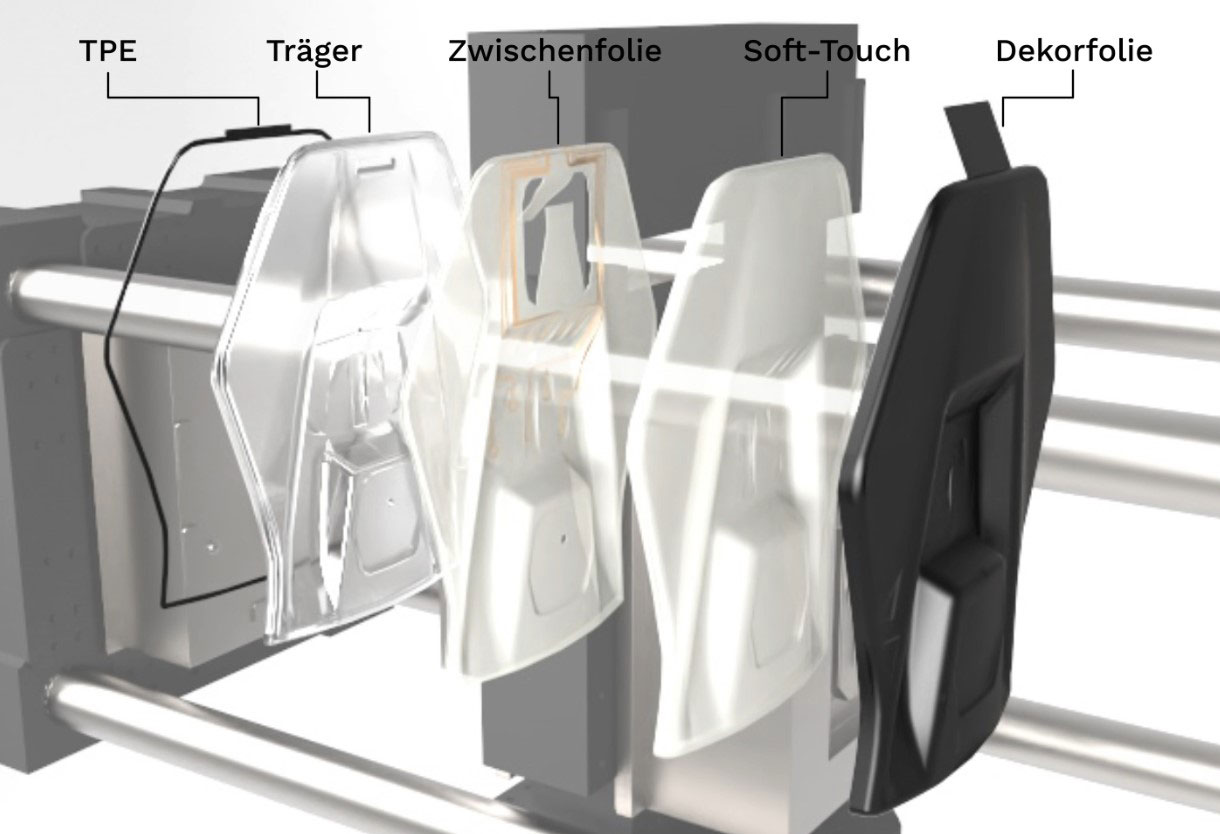
rechts: Explosionsdarstellung des Demonstratorbauteils bestehend aus den drei spritzgegossenen Komponenten (TPE-Dichtlippe, Träger und Softtouchkomponente) und aus den funktionalisierten Zwischen- und Dekorfolien (Quelle: © Neue Materialien Bayreuth GmbH)
Dazu wurden neuartige thermoplastische Materialien mit spezifischer Druck- und Schubhaptik entwickelt, welche für eine ansprechend weiche, der menschlichen Haut ähnliche Haptik sorgen. Dabei wurde zu Beginn der Materialentwicklung die „Zielhaptik“ im Rahmen einer Probandenbefragung ermittelt und diese messtechnisch in objektive Referenzwerte übersetzt, welche für die Weiterentwicklungsschritte Orientierung gaben.
Die Fertigung des Bauteils erfolgt in einem maßgeschneiderten, automatisierbaren 3‑Komponenten-Spritzgießprozess. Die speziell hierfür entworfene Werkzeugtechnologie ermöglicht dabei das Zwischenspritzen der Weichkomponente zwischen die beiden Funktionsfolien. Durch den neu entwickelten Foliendirektbeschnitt im Werkzeug wird das Maß an Prozessintegration noch zusätzlich erhöht.
Durch die speziell entwickelten funktionalisierten Folien lässt sich das in die Mittelkonsole integrierte Bauteil anschließend direkt in die Fahrzeugelektronik einbinden und sorgt für intuitive Bedienbarkeit und ein hochwertiges Seamless-Surface.