Die steigenden Ansprüche an Produkte bezüglich Qualität, Kosten und Zeit stellen für die Produktionstechnik wachsende Herausforderungen dar. Großes Potenzial bietet dabei das additive Fertigungsverfahren. Bei diesem schichtbasierten Verfahren entstehen Bauteile durch selektives Verschmelzen einzelner Pulverlagen.
Um kostengünstige, komplexe Strukturen zu fertigen, muss die gesamte Prozesskette hinsichtlich Fertigungskosten, -zeit und -qualität optimiert werden. Daher gilt es, das Potenzial für die Senkung der Materialkosten bei der Pulverherstellung zu identifizieren. Hierbei wird die Pulverherstellung in drei Verfahren eingeteilt: gasverdüst, plasmaverdüst, HDH. Ziel des Forschungsvorhabens war es, die bestmögliche Methode für die additive Fertigung ausfindig zu machen.

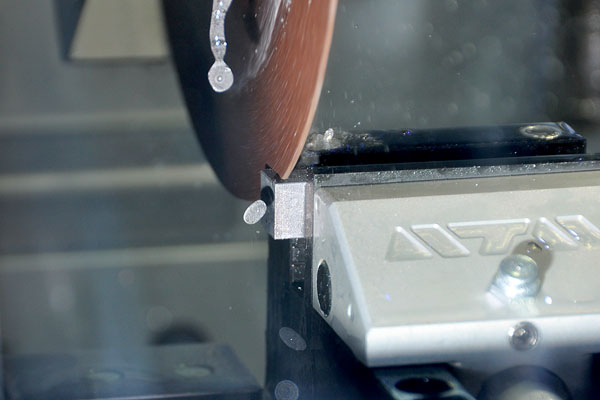
rechts: Probenpräparation zur Bestimmung der Restporosität (Quelle: Fraunhofer Institut für Werkzeugmaschinen und Umformtechnik (IWU), Projektgruppe Ressouceneffiziente mechatronische Verarbeitungsmaschinen (RMV) Prozesskette additive Fertigung)
Das Forschungsprojekt wurde in drei Phasen gegliedert. Die erste Phase bildete die Herstellung und Charakterisierung von Titan-Pulvern. In der zweiten Phase wurden Probekörper additiv gefertigt. Hierbei wurden die Prozessparameter für jede Pulversorte so variiert, dass eine minimale Restporosität im Bauteil resultierte. Die dritte Phase bildete die multikriterielle Bewertung, die neben den technischen Punkten auch wirtschaftliche Komponenten berücksichtigte.
Es konnte gezeigt werden, dass sich die untersuchten Herstellverfahren in drei Preis- und Qualitätsklassen einordnen lassen. Das plasmaverdüste Pulver zeigte eine sehr hohe Qualität bei sehr hohen Herstellkosten. Das im HDH-Verfahren hergestellte Material ist kostenseitig sehr lukrativ, jedoch auf Grund der Kornform nicht für die additive Fertigung geeignet. Die Alternative zu den beiden Verfahren bildet das gasverdüste Pulver. Es besitzt eine ausreichende Qualität für die additive Fertigung und ist günstiger als das plasmaverdüste Pulver.