Im Fokus des Forschungsvorhabens stand ein neuartiger einstufiger 3D-Druck mit besseren mechanischen und thermischen Eigenschaften als das bisherige Verfahren.
Die zunehmende Individualisierung von Produkten bei sinkender Produktlebensdauer und die gleichzeitige Forderung nach niedrigeren Kosten führt zu der Notwendigkeit, schnell und aufwandsarm Bauteile in Kleinserie herstellen zu können. Additive Fertigungsverfahren, im speziellen der 3D-Druck, bieten ein hohes Potenzial, diesen Anforderungen gerecht zu werden. Über einen Druckkopf wird Flüssigkeit auf ein Kunststoffpulverbett aufgebracht, was eine gezielte Verfestigung hervorruft. Da die Bauteile vor Projektbeginn eine hohe Porosität aufwiesen, war eine nachgelagerte Behandlung notwendig. Durch eine Infiltration mit z. B. Epoxidharz und einem Aushärteprozess konnte die Festigkeit der Bauteile erhöht werden.
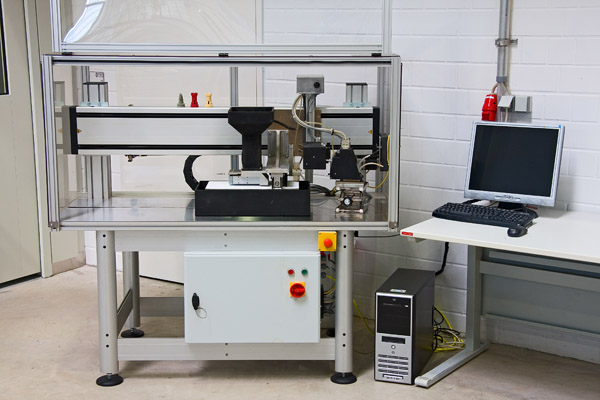
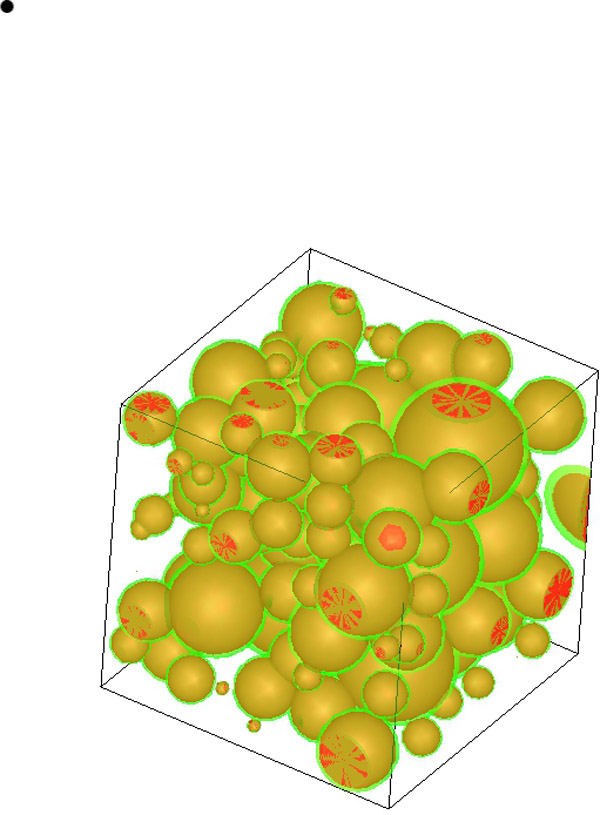
rechts: Schematisches Modell der Materialstruktur (Quelle: Technische Universität München, Institut für Werkzeugmaschinen und Betriebswissenschaften (iwb) und voxeljet Technology GmbH)
Das Ziel des Projekts AktiPol war neben der Realisierung eines neuen Anlagenkonzeptes die Entwicklung eines einstufigen Druckprozesses. Eine Verbesserung der mechanischen und thermischen Eigenschaften wurde durch eine aktivierte und möglichst weitgehende Polymerisation erreicht. Des Weiteren wurde die Integration mechatronischer Komponenten oder weiterer lokal determinierter Eigenschaften untersucht.
Im Projekt wurden die Anforderungen an den Prozess, die Anlage und das Produkt sowie die Prozessgrundlagen der Werkstoffe analysiert und diese für eine mögliche Verarbeitung mittels 3D-Druck qualifiziert. Auf Basis dieser Ergebnisse wurden ein Anlagenkonzept und eine Steuerungssoftware entwickelt. Mithilfe von experimentellen Untersuchungen fand im Anschluss eine Anpassung und Optimierung des Anlagen- und Werkstoffkonzepts statt. Eine Verifizierung mithilfe einer Multiskalen-Simulation schaffte ein besseres Verständnis für die beim 3D-Druck im Material entstehenden Mikrostrukturen und im Makro-Bereich auftretenden Effekte wie Verzug und Schrumpfung.