Traditionell werden Katalysatoren großtechnisch überwiegend als regellose Schüttungen einfacher Formkörper (Pellets, Extrudate, Tabletten) eingesetzt. Die heutigen Fertigungsverfahren für diese Formkörper ermöglichen ausschließlich einfache äußere geometrische Strukturen und nur eine sehr eingeschränkte Gestaltung der Geometrie des Formkörperinnenraums.
Mit Blick auf die Optimierung des Stoff- und Wärmetransports stellt die Dehydrierung von flüssigen organischen Wasserstoffträgern (Liquid organic hydrogen carrier, LOHC) eine besonders herausfordernde katalytische Reaktion dar. Dies ist vor allem begründet in der immensen Gasfreisetzungsrate der Reaktion bei gleichzeitig hohem Wärmebedarf zur Deckung der endothermen Reaktionsenthalpie.
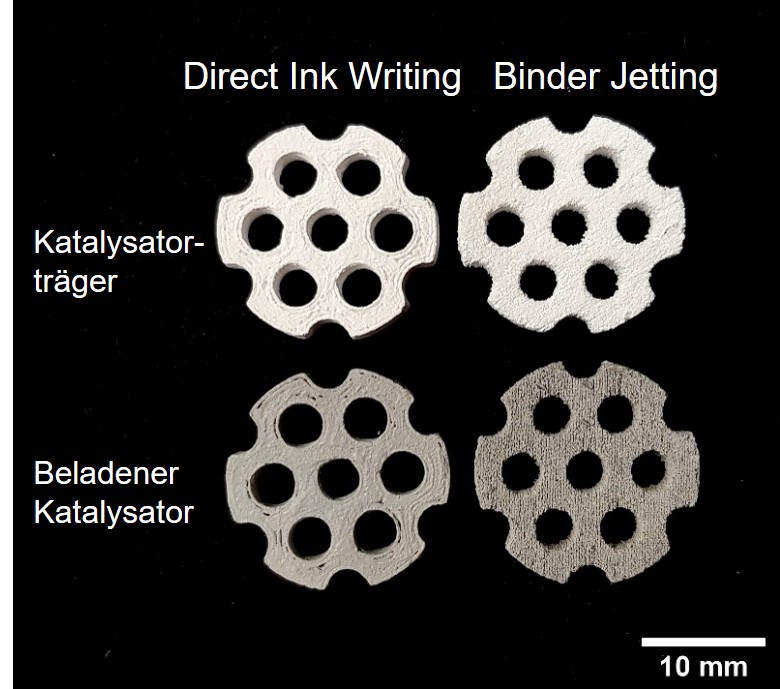
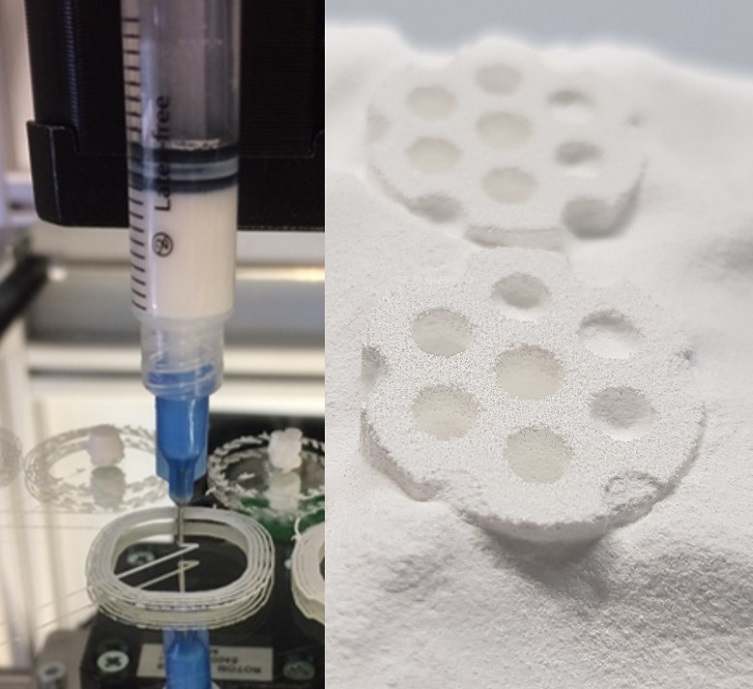
rechts: Pastenbasiertes DIW (links) und pulverbasiertes BJ-Verfahren (rechts) (Quelle: TUM / Paula Großmann, Hanh My Bui)
Ziel des Projekts „3DKat“ war es, die additive Fertigung (3D-Druck) als neuartige Formgebungsmethode mit der heterogenen Katalyse zu verbinden, um die katalytische Performance in der LOHC-Dehydrierung zu steigern.
Im Projekt konnten über das pastenbasierte 3D-Druckverfahren „Direct Ink Writing“ und das pulverbasierte „Binder Jetting“ geeignete Katalysator-Träger aus Aluminiumoxid hergestellt werden. Dabei konnten sowohl der Einfluss unterschiedlicher Katalysatorgeometrien auf die Dehydriergeschwindigkeit als auch Unterschiede zwischen den beiden Druckverfahren herausgearbeitet werden. Beide Formen konnten im Test die Leistung des kommerziellen Katalysators um etwa 50 % übertreffen.