Der Prototypenbau von transparenten, dreidimensional geformten Scheiben stellt die Industrie zunehmend vor Herausforderungen. Die Kostenminimierung durch den Verzicht auf komplexe Werkzeuge, die Verkürzung der Herstellungszeiten sowie ein weitaus geringerer Energiebedarf für die Produktion der Prototypen waren die Antriebsfeder für die Entwicklung des 3D-Formers.
Im Fokus der Entwicklung standen Prototypen aus transparenten Werkstoffen, deren Anwendung im Bereich der Medizintechnik liegen, sowie die Erzeugung von Windschutzscheiben im automotiven Umfeld und Flugzeugbau. Der wesentliche Vorteil des verwendeten Verfahrens liegt im kompletten Verzicht auf den Einsatz eines statischen Werkzeugs.
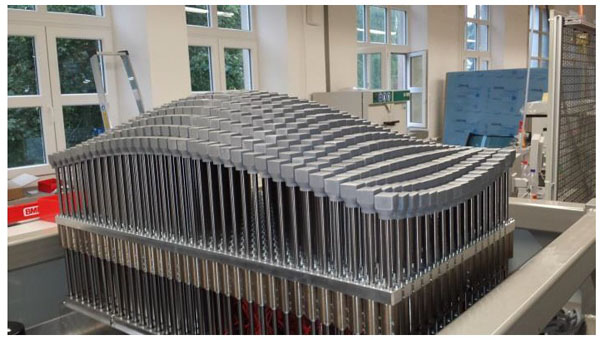
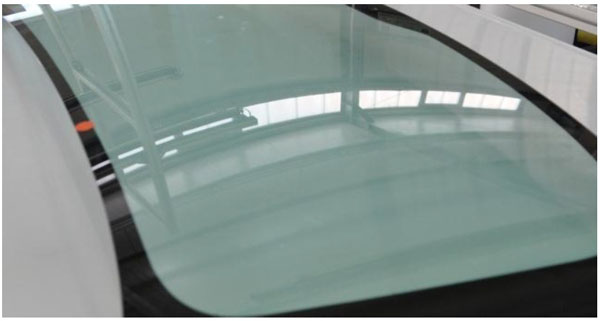
rechts: Prototyp einer Scheibe (Quelle: Technische Universität München, Lehrstuhl für Aerodynamik und Strömungsmechanik)
Herzstück der Anlage zur Formung der Werkstücke sind einzeln anzusteuernde Stempel, die eine theoretische Realisierung beliebig geformter Flächen ermöglichen. Die Schwerpunkte des Projekts waren die Entwicklung eines geeigneten Verfahrens zur Umformung von Scheibenmaterialien ohne Einsatz von statischen Werkzeugen, das Erzielen einer hohen Wiederholgenauigkeit bei mehrmaliger Verwendung der gleichen Werkstückformen, die Entwicklung und Anfertigung verschiedener Stempelformen zur Krafteinbringung auf das erwärmte Werkstück und die Fertigung einer Anlage zur Umformung der Ausgangswerkstücke.
Die technische Herausforderung ergab sich vor allem aus der für den Formungsprozess benötigten Werkstücktemperatur und dem damit verbundenen Fließen des Werkstoffes. Wenngleich aktuell noch kein abschließendes Ergebnis erzielt worden ist, zeigt die Anlage doch das enorme Potenzial und die Vorteile des eingesetzten Verfahrens. Die nachfolgenden Aufwände müssen daher der eingesetzten Stempelform sowie der genauen Einstellung der Prozesstemperatur dienen.