Im Fokus des Forschungsprojekts „ÖKOXAL“ stand die Energieeffizienz in der Galvanotechnik. Durch den Einsatz des Pulse Platings und eines innovativen Kühlkonzepts konnten in der Hartanodisation ca. 60 % Energie eingespart werden.
Aluminium ist einer der meistverwendeten Werkstoffe im Leichtbau. Einschränkungen bei der Verwendung gibt es lediglich durch seine geringe Verschleiß- und Korrosionsbeständigkeit. Dieser Mangel lässt sich durch das Aufbringen von beständigen Schichten durch Hartanodisation beseitigen. Die Hartanodisation gehört jedoch zu den energieintensivsten Verfahren innerhalb der Galvanotechnik, was bei steigenden Energiekosten und der zunehmenden ökologischen Fokussierung die Entwicklung effizienterer Verfahren bedingt.
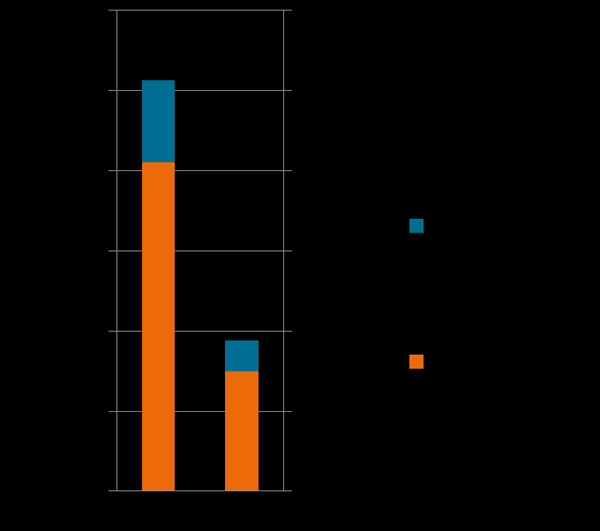
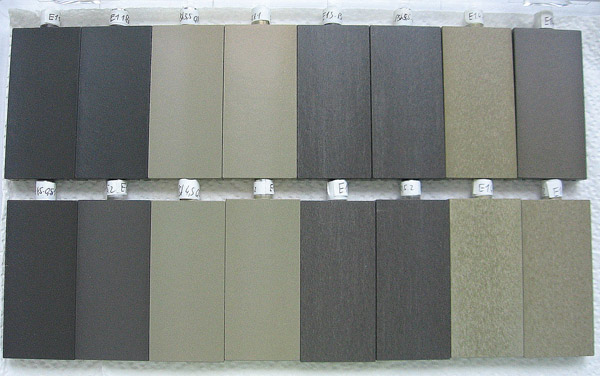
rechts: Ausgewählte Aluminiumlegierungen, mit Pulsanodisation beschichtet (Quelle: Galvano Weis GmbH & Co. KG, Galvanische Werkstätte)
Ziel des Projekts „ÖKOXAL“ war die Einsparung von 25 % der Gesamtenergie gegenüber dem konventionellen Hartanodisieren. Der Erhalt der hervorragenden Eigenschaften der Hartanodisierschichten mit Hilfe des entwickelten Verfahrens war dabei Voraussetzung. Der Ansatz des Projekts beruhte darauf, durch Einsatz der Pulsanodisation die sehr niedrigen Elektrolyttemperaturen bei der konventionellen Hartanodisation deutlich zu erhöhen. Gleichzeitig verringert sich durch die Pulsanodisation der Eintrag thermischer Energie in das Bad, wodurch zur weiteren Effizienzsteigerung wesentlich höhere Abscheidegeschwindigkeiten möglich waren.
Die geänderte Verfahrenstechnik ermöglichte durch die Erhöhung der Badtemperatur ein innovatives Kühlkonzept. Zukünftig wird mit einer Hochtemperaturwärmepumpe Kühlenergie und nutzbare Prozesswärme bereitgestellt. Die grundlegende Forderung nach mindestens gleichwertigen Schichteigenschaften wie Härte, Schichtdicke, Verschleiß und Rauheit konnte vollumfänglich erfüllt werden. Die energetischen Einsparziele wurden mit einer Gesamteinsparung von ca. 60 % gegenüber dem konventionellen Verfahren weit übertroffen.